Managing Workplace Health and Safety Risks: the Hierarchy of Control
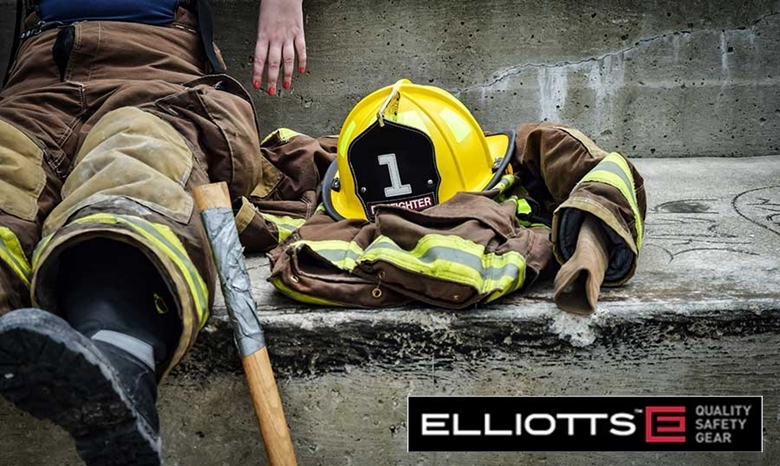
Workplace Health and Safety Risks Management Guidelines
According to this Safe Work Australia factsheet, there are 4 steps that guide Workplace Health and Safety risk management. These have been developed to ensure maximum employee safety and effective risk control.
1. Identify Hazards
The first step in risk management is finding equipment and circumstances that could potentially cause harm to people. These involve work tasks and how they are performed, equipment, materials and substances used, and also the physical work environment and its design and management. To find potential risks you should perform a thorough inspection of the workplace, consult your workers and review information records.
2. Assess Risks
Risks need to be assessed whenever there is uncertainty about what would happen if someone is exposed to a safety hazard, or if there’s uncertainty about the effectiveness of existing risk control measures. Whenever new practices or changes to the workplace are introduced, or when a work task involves a number of safety risks there is a greater risk of limited understanding about the interaction of these risks or if they could potentially create a greater hazard, risk assessment measures need to be taken.
You need to consider what could happen if someone is exposed to hazards and how likely such dangerous situations are to occur. There are resources, such as this Safe Work Australia Code of Practice, that can guide you in risk assessment by providing you with all the right questions to ask and giving you examples that will help you determine what risk control measures are necessary.
3. Control Risks – using the Hierarchy of Risk Control
The most important thing in managing risks is to try and eliminate them completely whenever reasonably practicable, and when not possible, it is essential that risk is minimised so far as is reasonably practicable.
Note that some risks are easier to control than others, and they should all be studied and assessed separately. When solving such problems, it is required by the WHS Regulations that managers and duty-holders follow the hierarchy of risk control. This tool ranks risk control methods from the highest levels of safety and reliability to the lowest.
LEVEL 1
Eliminate the Hazard – Eliminate dangerous machinery whenever possible.
LEVEL 2
Substitute the Hazard – Implement safer alternatives whenever possible, e.g. have water-based paint instead of solvent-based paint.
Isolate the Hazard – Physically separate the hazard from people, e.g. install rails around holes in floors.
Use Engineering Controls – Use physical measures, e.g. use trolleys for heavy loads, electrical safety switches put in place etc.
LEVEL 3
Use Administrative Controls – Procedures to minimise hazards, e.g. use of signs, safety procedures when operating machinery, etc.
Use Personal Protective Equipment (PPE) – Ear muffs, goggles, masks, and gloves. They must fit properly and be used consistently. Make sure they were designed to cater to the specific hazards that workers are at risk of.
4. Review Control Measures
Risk control measures and procedures should be reviewed regularly and constantly improved on. Don’t wait until an accident happens, do your best to avoid hazards. And when they happen, keep records so you can reflect on them, make further improvements to your existing risk control measures and implement new ones whenever necessary.
CONTACT US
If you'd like to learn more about our work safety products or need expert advice on which safety gear to get for your requirements, feel free to get in contact with us at Elliotts Australia. We would be happy to assist you! Call us on 07 3265 2944 or send us a message.